¿Qué son los agujeros de alfiler y las discontinuidades?
Un recubrimiento protector es tan fuerte como su punto más débil, lo que pone en evidencia los graves peligros de cualquier brecha o discontinuidad posterior. Una discontinuidad en el recubrimiento puede tener consecuencias devastadoras, similares a las causadas por los puntos débiles de un recubrimiento protector. Los puntos débiles dejan al descubierto el sustrato subyacente, permitiendo el acceso a las fuerzas destructivas de la corrosión y la erosión, lo que en última instancia hace que el recubrimiento sea inútil. En la industria, estos se denominan “defectos”, es decir, una zona del sustrato que no se ha recubierto correctamente y que se presenta como una discontinuidad en la película del recubrimiento. Esto incluye defectos, espesores del recubrimiento inadecuados, inclusiones y agujeros de alfiler (poros), todos los cuales se registran como anomalías. A lo largo de este artículo, aclararemos algunos mitos en torno a los defectos y los agujeros de alfiler, al tiempo que analizaremos la detección de defectos y las soluciones utilizadas para corregirlos.
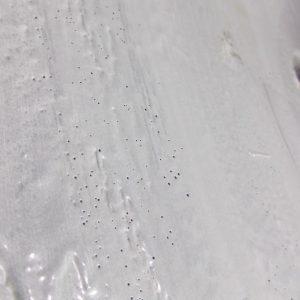
Discontinuidades infernales: la pesadilla de un ingeniero
La aparición de defectos se atribuye a un error del aplicador o a la falta de conocimientos sobre la aplicación de recubrimientos. Esto incluye el conocimiento de las condiciones ambientales, que afectan y generalmente dificultan la aplicación. La viscosidad del recubrimiento es una de las causas más comunes de las deficiencias, que se ve especialmente afectada por las condiciones ambientales. Una viscosidad imperfecta perjudica el éxito general de la aplicación. Las condiciones extremas de temperatura suelen provocar fluctuaciones en la viscosidad del recubrimiento, lo que dificulta la aplicación. Posteriormente, esto formará descuelgues y ondulaciones y, sin duda, provocará fallos o saltos en la estructura del recubrimiento.
Las características del recubrimiento, una vez aplicado, también pueden aumentar la probabilidad de que se produzcan vacíos una vez curado el recubrimiento. En primer lugar, una mezcla insuficiente o inadecuada de los componentes del recubrimiento puede crear zonas que no se curan, lo que provoca descascarillado, entre otros defectos del recubrimiento. Además, mezclar en exceso el recubrimiento antes de la aplicación puede combinar demasiado aire con el producto, creando una cantidad significativa de burbujas de aire.
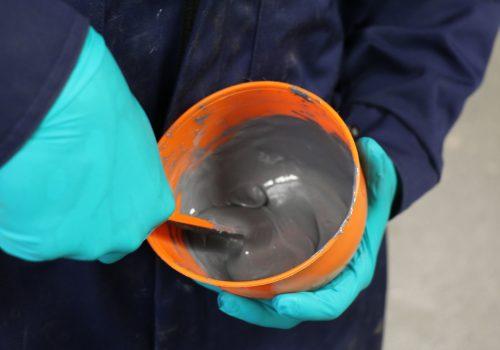
Predominantemente, los poros se forman cuando las burbujas de aire suben a la superficie del recubrimiento, estallan y no son reselladas por el propio recubrimiento. Estos pequeños agujeros pueden limitarse simplemente a la capa superior del recubrimiento o continuar directamente a través de dos capas, dejando al descubierto el sustrato. Al recubrir un sustrato con brocha, los aplicadores deben asegurarse de aplicar dos capas. Después de la capa inicial, la segunda capa debe aplicarse perpendicularmente a la capa original, cubriendo así cualquier vacío que pueda producirse. De lo contrario, es posible que no se cubran las discontinuidades existentes, como los poros.
Además, se producen importantes áreas de error en zonas de difícil acceso para garantizar la aplicación de una capa uniforme en todo el sustrato. En la práctica perfecta, los aplicadores deben utilizar técnicas de acceso por espejo para eliminar dudas sobre discontinuidades en lugares de difícil acceso.
Equipos y métodos de detección de poros y discontinuidades
Muchos de estos defectos no pueden detectarse visiblemente. Por ello, se utilizan determinados tipos de equipos para localizar anomalías en el recubrimiento. Dado que los recubrimientos son productos aislantes que protegen el sustrato metálico conductor, la comprobación de esta propiedad es el método más eficaz para detectar defectos. Utilizando la electricidad para localizar estas discontinuidades de la película, los detectores de defectos pasan una corriente sobre el recubrimiento, intentando crear un circuito cerrado con el sustrato que hay debajo.
Una anomalía puede identificarse utilizando instrumentos tanto de alta como de bajo voltaje; sin embargo, cada uno de ellos debe adaptarse específicamente a la aplicación, en función de diversas variables. Por ejemplo, las condiciones ambientales deben ser adecuadas para comprobar eficazmente la superficie, especialmente en lo que respecta a las condiciones de la superficie. Un recubrimiento seco y curado es esencial para obtener resultados positivos en las pruebas; de lo contrario, los residuos atrapados o las zonas no curadas aún presentes en el recubrimiento pueden proporcionar lecturas falsas.
Normalmente, se utiliza la prueba de esponja húmeda de bajo voltaje o la prueba de chispa de alto voltaje, y cada una tiene capacidades claramente diferentes en términos de funcionalidad. Evidentemente, la diferencia significativa está relacionada con el voltaje de los dos dispositivos; sin embargo, esto influye en el tipo de recubrimiento para el que se puede utilizar cada uno. Las directrices de los fabricantes indican que los comprobadores de esponja húmeda de bajo voltaje sólo se recomiendan para recubrimientos con un espesor máximo de 500 µm (micras). Para los revestimientos que se aplican con un espesor superior a 500 µm, deben utilizarse equipos de alto voltaje (suponiendo que el recubrimiento sea compatible).
Otra diferencia significativa tiene que ver con la forma en que detectan la presencia de discontinuidades. Los equipos de baja tensión utilizan el agua, como vía para la electricidad, para conectar con las zonas expuestas del sustrato. En cambio, el equipo de alta tensión es capaz de puentear la distancia entre el comprobador y el material conductor simplemente a través del aire. También hay diferencias de seguridad considerables, ya que el sistema de esponja húmeda que funciona a un máximo de 90 V no puede dañar ni al operario ni al recubrimiento, mientras que la versión de alta tensión que funciona a hasta 60.000 V, si no se maneja correctamente, puede dañar gravemente tanto al operario como al recubrimiento que se está probando.
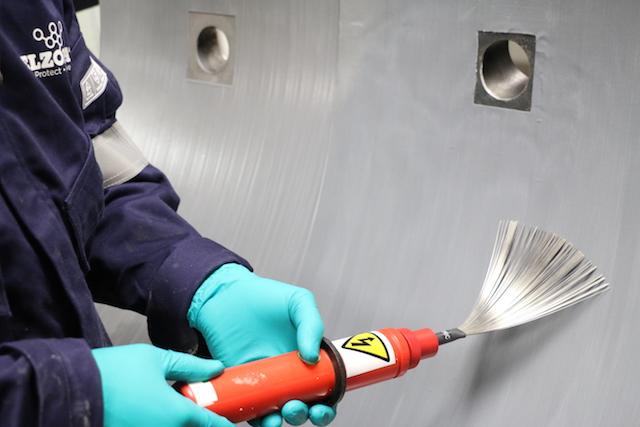
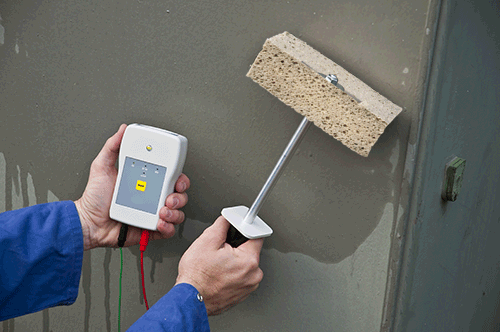
Problemas relacionados con la detección de poros y discontinuidades
Uno de los mayores problemas en torno a la detección de discontinuidades gira en torno a los ajustes de tensión y la rigidez dieléctrica. Cada recubrimiento tiene una rigidez dieléctrica, que determina la tensión específica que un recubrimiento puede soportar antes de empezar a romperse. Elegir entre comprobadores de alta y baja tensión, así como ajustar la tensión correcta para no causar más daños al recubrimiento, es crucial para evitar más daños al recubrimiento durante la detección de discontinuidades.
Para proporcionar características diferentes y propiedades adicionales a los recubrimientos, se añaden aditivos y cargas. Algunos de ellos consisten en cargas metálicas, que deben reconocerse antes de realizar cualquier prueba. Cuando nos enfrentamos a recubrimientos con rellenos metálicos, que pueden ser semiconductores, es preferible una técnica de método de ensayo de baja tensión, por ejemplo utilizando la técnica de la esponja húmeda. Por otro lado, pueden utilizarse equipos de prueba de alta tensión para discernir si un revestimiento con relleno no metálico tiene discontinuidades.
Como ya se ha señalado, a veces los agujeros son tan pequeños que restringen el paso del agua desde el comprobador de baja tensión hasta la superficie conductora situada debajo. En estos casos, los aplicadores utilizarán un surfactante para reducir la tensión superficial del agua. Al reducirse la tensión superficial, la solución puede penetrar en el agujero y reconocer eficazmente el defecto del recubrimiento.
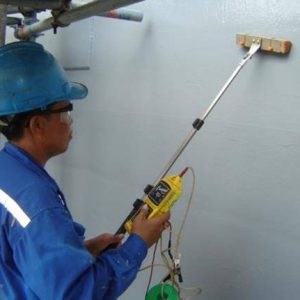
Restauración del recubrimiento
Las posibles técnicas de aplicación deficientes pueden eliminarse siguiendo directrices y procedimientos de aplicación de recubrimientos específicos. Para conseguir el mejor recubrimiento posible, libre de defectos potenciales como vacíos y poros, es necesario seguir la norma NACE SP0188. Como siempre, la seguridad es primordial cuando se utilizan equipos de esta naturaleza y, como parte de las directrices de la NACE, hay ciertas medidas que conviene recordar. Incluidas las comprobaciones de seguridad eléctrica, cuando se realizan pruebas de alta tensión es necesario realizar evaluaciones exhaustivas del entorno de prueba para garantizar que no haya elementos potencialmente explosivos. Además, una toma de tierra eléctrica completa del sustrato es de vital importancia para evitar DESCARGAS ELÉCTRICAS.
Las soluciones de reparación de discontinuidades dependen totalmente de si el recubrimiento puede renovarse o no. Si el recubrimiento tiene el espesor máximo, no se puede aplicar otro recubrimiento encima de la discontinuidad existente. La zona alrededor de la discontinuidad se delinea inicialmente con los bordes alisados hacia el defecto. Una vez completada, la zona puede someterse a un chorro de granalla ligero antes de aplicar un recubrimiento de sustitución.
Por otra parte, si el recubrimiento está por debajo del espesor máximo, se puede aplicar otro recubrimiento. Simplemente raspando la superficie antes de una aplicación sucesiva, la discontinuidad puede cubrirse y eliminarse con éxito. Una vez finalizada la reparación, debe realizarse otra prueba de discontinuidad para establecer que la reparación ha sido satisfactoria. En particular, la zona de reparación es el único lugar que debe probarse para evitar tensiones excesivas contra la integridad del recubrimiento.
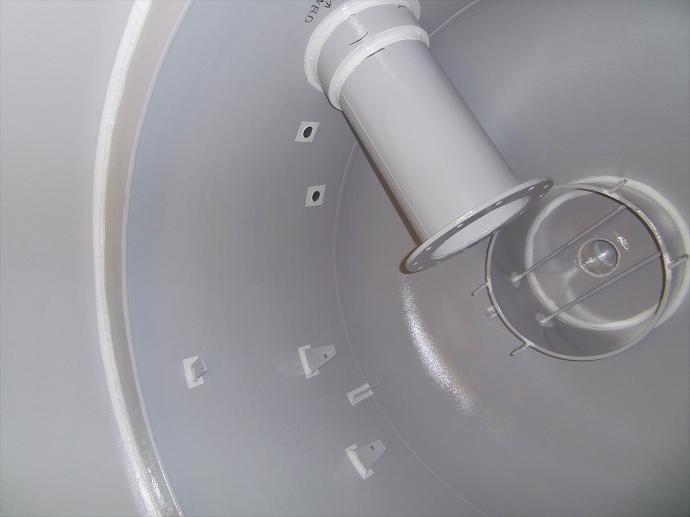
AGENDA UNA VISITA GRATIS
¡AHORA!
Desde 1987 venimos brindando asistencia técnica industrial, la solución a sus necesidades de mantenimiento.